Permanent magnet rotor e1655961736623.jpeg.
When permanent magnet synchronous motor is running at ultra-high speed, the tensile strength of permanent magnet is far lower than the compressive strength, and it is unbearable to withstand the large centrifugal tension caused by rotation. Generally, adding the non-magnetic alloy sleeve outside the permanent magnet is the protective …
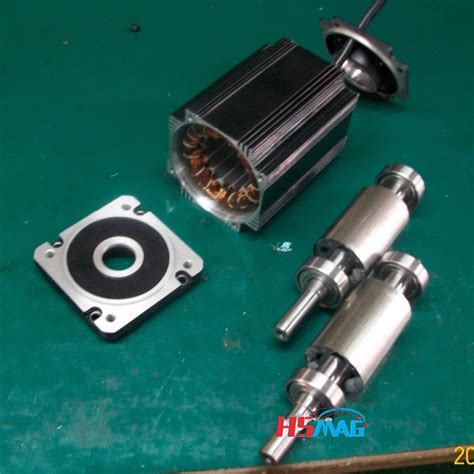
Synchronous motor. Miniature synchronous motor used in analog clocks. The rotor is made of permanent magnet. Small synchronous motor with integral stepdown gear from a microwave oven. A synchronous electric motor is an AC electric motor in which, at steady state, [1] the rotation of the shaft is synchronized with the frequency of the supply ... the permanent magnet Once the permanent magnet is inserted into a slot of the rotor core, it generates a stress-point within the core as a result of centrifugal force. If the permanent magnet slips out of the slot within the rotor core during operation of the drive motor as a result of this centrifugal force, the permanent magnet, the rotor core, or …2.1 Electrical Characteristics. The equivalent circuit of a PMDC motor is shown in Fig. 1. The supply voltage and the current are given. The circuit consists of an induced voltage (Vi) in series with an armature resistor (Rarm) and inductance (Larm). The rotation of the ux generates the induced voltage. A new technique for high performance and robust speed control of permanent magnet synchronous motor (PMSM) using a mixed non-linear H∞ and Sliding Mode Control (SMC) is applied.addition to the magnet torque, thus improving the efficiency. In addition, the IPMSMs provide more rotor robustness as magnets are embedded in the rotor laminations; hence, no additional retention sleeving is required. Various IPMSM technologies have been studied in the literature. In [3], the V-shape, the U-shape, the spoke-type and the
Rmr reluctance of the magnet to rotor back iron leakage flux Rmm reluctance of the magnet to magnet leakage flux Rg reluctance of the airgap rb mean radius of stator winding, i.e. (ri + ro)/2 ri inner radius of magnet ro outer radius of magnet Sc area of one conductor cross-section Sp arc length of one coil pitch at the outer radius ro of the ...The actual power capacity of permanent magnet synchronous machine for electric vehicles is usually limited by rotor temperature, ... Usually, measuring the temperature of the rotor permanent magnet is very difficult by equipping sensors to rotate the body directly. Some common techniques include slip rings, ...
Rmr reluctance of the magnet to rotor back iron leakage flux Rmm reluctance of the magnet to magnet leakage flux Rg reluctance of the airgap rb mean radius of stator winding, i.e. (ri + ro)/2 ri inner radius of magnet ro outer radius of magnet Sc area of one conductor cross-section Sp arc length of one coil pitch at the outer radius ro of the ...Yu S B, Tang R. Electromagnetic and mechanical characterizations of noise and vibration in permanent magnet synchronous machines. IEEE Trans Magn, 2006, 42: 1335–1338. Article Google Scholar Zuo S, Lin F, Wu X. Noise analysis, calculation, and reduction of external rotor permanent-magnet synchronous motor.
Jun 9, 2022 · To solve the problem of tension stress caused by centrifugal force and caused by high-speed operation of permanent magnet (PM) rotor, a FeCo-based PM rotor structure model is proposed. Based on the thick-walled cylinder theory, the uniform analytical calculation formulas of strain field, displacement field, and stress field of high-speed permanent magnet rotor are derived, and the stresses of ... The inner rotor and outer rotor permanent magnet design were made comparatively to GSA and GSA-PSO algorithms to optimize the design. GSA-PSO was found to be more efficient than GSA. The Outer Rotor PMSG (ORPMSG) weight was reduced by 32% and rotor weight by 13%, resulting in a design with fewer wind …Since the pole arc coefficient of the rotor permanent magnet is 0.5, according to Ref. 28, the magnetomotive force generated by the permanent magnet is equal to that generated by the adjacent FMP.Dec 1, 2017 · In their work, a range of electric machine options are considered and it is concluded that a synchronous machine with a permanent magnet (PM) rotor will be the most efficient and power dense. In addition to applications in turbocharging, Gerada [ 3 ] highlight an increasing demand for high-speed electrical machines in flywheel energy storage ... High-speed or ultra-high-speed permanent magnet synchronous motors (PMSMs) have a strong trend of application in modern industry due to those simple structures and high power density. 1,2 For high-speed motors or generators, the rotor speed is normally above 30,000 r/min even may exceed 100,000 r/min. Designs of such high …
2 Rotor system dynamics modelling of high-speed PM motor 2.1 Support characteristics of active magnetic bearings (AMBs) To make the rotor reach a high speed, the use of non-contact magnetic bearing or air bearing is required. First the rotor critical speed analysis needs to study the support characteristics of rotor-bearing system.
Summary. PM (Permanent Magnet) Type: uses permanent magnets, moderate torque, low to mid-speed. VR (Variable Reluctance) Type: toothed rotor/stator, low torque, mid to high speed. Hybrid Type: combines permanent magnets and teeth, good combination of torque and speed.
Aiming at the rotor strength problem of high speed permanent magnet synchronous motor (HSPMSM), a design method for maximum outer diameter of permanent magnet is proposed. Firstly, on the basis of mechanics of materials, the stress analytical model of HSPMSM rotor with anisotropic material is established. Then, the …The SPMSM has the permanent magnets fixed on the surface of the rotor leading to a symmetrical radial air-gap reluctance path between the rotor and the stator core. The IPMSM has the permanent magnets inserted inside the rotor core leading to a non-symmetrical radial air-gap reluctance path between the rotor and the stator core. External rotors of “outrunner” type. Rotors with additional bandage (Polyglas, Kevlar, carbon) Rotors with protecting sleeve. Contact us. Jan Kratochvil ml. +420 607 570 823 [email protected]. We will be happy to cooperate on development and manufacturing of rotors with permanent magnets, please contact our specialist. Leave …where Φ is the magnet flux crossing the air gap, R is the total reluctance through the flux paths and θ is the rotor angle. It is clear that if the reluctance R does not vary as the rotor rotates, then the cogging torque T cog is zero. From this point of view, the cogging torque can be improved by changing the V-shape rotor structure variables …Jan 10, 2022 · The rated power and speed of the permanent magnet grinding electric spindle are 7.5Kw and 950r/min, respectively.The main parameters of the PMGES are as follows, the rotor mass is m = 5.66 kg; the rotor radius is R = 0.072 mm; the axial length of the air gap is L = 0.178 mm, nominal air gap length is δ 0 = 3 × 10 −3 m, air permeability is ... 2.2 External rotor permanent magnet motor rotor air gap magnetic field When the motor is running at no load, the air gap magnetic field is provided by the permanent magnet alone. The generated magnetic field rotates together with the rotor and the rotational speed is synchronous speed.
Measure Skewing Angle. MagScope software makes it easier than ever to measure the skewing angle of skewed permanent magnet rotors, enabling the detection of skewing angle deviations. The right figure shows an example of the step skew on an IPM (Interior Permanent Magnet) rotor, represented in a cross-section graph with automatic zero-crossing ... Rotor position information is necessary for the control of a permanent magnet synchronous motor (PMSM) and position sensorless control is the trend for its low cost, high reliability and space-saving.@article{osti_1349258, title = {Brushless and Permanent Magnet Free Wound Field Synchronous Motors for EV Traction}, author = {Ludois, Daniel C. and Brown, Ian}, abstractNote = {This final report presents an advanced electric motor design for vehicles. The motor is a wound rotor synchronous machine whose rotor coils are …Jun 23, 2022 · The rotor overtemperature caused by losses is one of the important issues for the high-speed electrical machine. This paper focuses on the rotor loss analysis and CFD-thermal coupling evaluation for 105 kW, 36,000 r/min HSPMSM. Three types of sleeve materials as carbon-fiber, Titanium alloy, and stainless steel are introduced in this paper, researching the effects of sleeve conductivity ... For high-speed permanent magnet synchronous motor (PMSM), its efficiency is significantly affected by the performance of permanent magnets (PMs), and the phenomenon of demagnetization will occur with the increase of PM temperature. So, the temperature detection of PMs in rotor is very necessary for the safe operation of PMSM, …
Since the pole arc coefficient of the rotor permanent magnet is 0.5, according to Ref. 28, the magnetomotive force generated by the permanent magnet is equal to that generated by the adjacent FMP.1 Introduction. Flux-switching permanent-magnet (FSPM) motors have advantages such as high-power and -torque density, high efficiency and simple and robust mechanical structure in the rotor [1-4].These motors have bipolar flux linkage and sinusoidal back-electromotive force (EMF) [].In FSPM motors, because of the placement of …
Dec 15, 2023 · Interior permanent magnet (IPM) motors in traction applications often employ discrete rotor skewing constructions to reduce torsional excitations and back-EMF harmonics. Although skewing is very effective in reducing cogging torque, the impact on torque ripple is not well understood and can vary significantly over the operating envelope of a motor. Skewing also leads to the creation of a non ... A commercial traction motor (Prius 2010), designed with Nd-Fe-B magnets for maximum power 60 kW and maximum speed 13,500 rpm, is used as the baseline for comparing the HRMM design. The HRMM design shows comparable performance with the commercial design for the given speed range with ~ 50% reduction in critical rare earth …The equivalent magnetic circuit (EMC) is employed both to design the mechanical parameters of the rotor while considering nonlinear magnetic saturation effect and to analyze the magnetic characteristics of the air-gap of the motor. This paper considers the design and performance evaluation of interior permanent magnet …Aiming at the rotor strength problem of high speed permanent magnet synchronous motor (HSPMSM), a design method for maximum outer diameter of permanent magnet is proposed. Firstly, on the basis of mechanics of materials, the stress analytical model of HSPMSM rotor with anisotropic material is established. Then, the …Sep 17, 2020 · Differently from the surface-mounted permanent magnet (PM) synchronous motors, there is an asymmetry of the reluctance between the d-axis and the q-axis, in which saliency can be used to produce reluctance torque in addition to the magnet torque, thus improving the efficiency. In addition, the IPMSMs provide more rotor robustness as magnets are ... A permanent magnet is a material that can provide magnetic flux when magnetized with an applied magnetic field and its magnetism capability is characterized by two key parameters: remanence and coercitivity. In general, the intrinsic coercitivity of a permanent magnet (Hcj ) is greater than 300kOe (in the CGS unit) or 24kA / m (in the SI unit). This paper is focused on the optimal design, simulation, and experimental testing of a counter-rotating double-rotor axial flux permanent magnet synchronous …Apr 1, 2012 · In fact, as weâ ll explore, the major difference between PMAC and permanent magnet DC motors is that the faster a PMACâ s rotor spins, the higher back-EMF voltage is generated.
1. Introduction. At present, the low-speed high-torque transmission system has vast application prospects in the application fields of ship propulsion, lifting, mining and oil field exploitation [1].Permanent magnet motors can maintain good performance in a wide range of load changes, so they have received extensive attention in low-speed and large …
The designed external rotor PMSynRM motor is shown in Fig. 1.PMSynRM is designed to be mounted in the wheels of the EVs. The design parameters of the designed motor are given in Table 1.The d-axis and q-axis magnetization inductances play an important role in determining the electromagnetic performance of the motor [] and this is …
Oct 6, 2023 · The rotor of the HSPMSM adopts a solid cylindrical permanent magnet rotor with the parallel magnetization of two poles. The excitation magnetic field of the permanent magnet is a standard sinusoidal magnetic field, which can provide a large magnetic potential, which is convenient for the design of large air gaps and is conducive to ventilation and heat dissipation. The permanent magnet (PM) brushed DC-motor only has one winding: that is of the armature on rotor, whereas the field winding (on the stator) is replaced by a permanent magnet. This is the class of brushed DC-motor that we study in this chapter. PM brushed DC-motors can be found in a wide range of applications.Apr 8, 2022 · This paper proposes two structures of dual-stator permanent-magnet vernier machines (VMs) for high-torque low-speed applications. The proposed structures consist of dual-sided rotor which is sandwiched by inner and outer stators. These topologies include 22 and 46 consequent-pole magnets in the rotor and 24 and 48 stator slots for Design A and Design B, respectively. Design A is an improved ... Jan 31, 2017 · Understanding permanent magnet motors. A permanent magnet (PM) motor is an ac motor that uses magnets imbedded into or attached to the surface of the motor’s rotor. This article provides an elementary understanding behind the terminology, concepts, theory, and physics behind PM motors. Jan 8, 2021 · The permanent magnet is axially magnetized; meaning that the north and south poles alternate and are on the same axis as the motor shaft. When current is applied to windings, poles on the stator are magnetized and align with the opposite poles from the permanent magnet rotor. For example, north poles would align directly across from south poles. The prototype machine is an axial-flux permanent-magnet machine with a two-rotor–one-stator configuration. The nominal power of the machine is 300 W and the nominal rotational speed is 500 rpm. The magnets are neodymium iron boron magnets. Twelve magnets are mounted on the rotor surface and 12 magnets buried on the rotor (Fig. 12a).Nov 12, 2020 · A double-sided permanent magnet rotor with a single stator [2, 3] can offset the axial attraction and increase the output power at the cost of an increased weight. The double-sided permanent magnet rotor design can also reduce bearing wear and noise problem compared with a single-sided structure, which thus increases the generator reliability. reluctance, thus creating a magnetic pull to rotate the rotor. PM motors are driven by the interaction of the magnetic field generated by the permanent magnets and the rotating magnetic field generated by the stator winding. The characteristics of these high-speed motors are shown in Table1[61]. As can be seen from Table1, the high-speed …Dec 2, 2022 · This paper presents an analytical method for calculating rotor stresses of high-speed surface-mounted permanent magnet synchronous motors (SPMSMs) with segmented permanent magnets (PMs), the pole-arc coefficient, fillings between poles, and material anisotropy are accurately considered. Afterward, the rotor stresses with different retaining sleeves and fillings are compared, the variation laws ... This paper compares two flux-switching machines, namely, one stator permanent magnet flux-switching machine and one rotor permanent magnet flux …In this work, different analytical methods for calculating the mechanical stresses in the rotors of permanent magnet machines are presented. The focus is on interior permanent magnet machines. First, an overview of eight different methods from the literature is given. Specific differences are pointed out, and a brief summary of the …
In order to get rid of the bulky and lossy differential gears and to enhance the system robustness, the magnetic differential (MagD) system is proposed after the mechanical differential (MechD) and electronic differential (ElecD) systems. The MagD system is mainly composed of the double-rotor (DR) stator-permanent-magnet (PM) …An integrated-starter-generator (ISG) is a key component of hybrid electric vehicles (HEVs), which starts the engine as a motor and generates electric power as a generator according to operational conditions and system requirements [1,2,3].At present, conventional permanent magnet (PM) brushless machines with PMs in the rotor are …This control method can control the AC permanent magnet servo motor as a DC permanent magnet motor in a sense. According to Equations (1)–(3), the second-order dynamic equation of the position ring of the PMSM is expressed as follows: (4) { θ ˙ = ω ω ˙ = b i q + d (4) where b = 1.5 p n ψ f / J is a disturbance composed of unknown friction …The most obvious performance difference is that a PMAC motor rotates at the same speed as the magnetic field produced by the stator windings, meaning it is a synchronous machine. If the field is “rotating” at 1800 rpm, the rotor turns at the same speed. An induction motor, on the other hand, is considered an asynchronous machine. Instagram:https://instagram. zafpercent27s party storelvquntaalcdames sneakers blackstone cw96 bruin leer met wol.xhtmlverizonvireless Abstract: For the high-frequency permanent magnet electrical machine, a reasonable mechanical aspect design is crucial to meet its stability and reliability. This study focuses on the accurate modelling and analysis of the natural frequencies and modes of the rotor assembly for a designed and manufactured 100 kW 32,000 r/min motor.Mar 29, 2018 · For the high-frequency permanent magnet electrical machine, a reasonable mechanical aspect design is crucial to meet its stability and reliability. This study focuses on the accurate modelling and analysis of the natural frequencies and modes of the rotor assembly for a designed and manufactured 100 kW 32,000 r/min motor. cars for sale in sacramento under dollar2 000boletin de visas julio 2022 The main objective of this paper is to design and analyze the performance of in-wheel outer rotor permanent magnet synchronous motor (PMSM) used in electric vehicles based on a previously designed ... bjpercent27s careers near me Apr 17, 2022 · Crider, J.M., Sudhoff, S.D.: An inner rotor flux-modulated permanent magnet synchronous machine for low-speed high-torque applications. IEEE Trans. Energy Convers. 30(3), 1247–1254 (2015) CrossRef Google Scholar Reism, K., Binder, A.: Development of a permanent magnet outer rotor direct drive for use in wheel-hub drives. A new technique for high performance and robust speed control of permanent magnet synchronous motor (PMSM) using a mixed non-linear H∞ and Sliding Mode Control (SMC) is applied.Permanent Magnet Motors - External Rotor. The W series external-rotor permanent magnet motor combines the high strength alloy material with the patented one-piece fan …